Nice neat layout skier - puts mine to shame, although I am stuck in older technology

Here's my 2-cents...
Cable runs
A similar idea for supporting cables with hardware-store hooks spaced every 40cms or so.
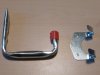
Not as neat as yours as the wires are exposed - they also need holding in place with tie wraps to stop them drooping and also when the studio grew and the hooks started overflowing. The room has a 15cm skirting board so can get two parallel runs using the small hooks one above the other to keep audio & non-audio cables apart. The larger L-shaped hooks are for the massive (& heavy!) cable runs from the mixer & recorder to the patch panels.
Cable clamps
These are custom-made slabs of steel bolted to the QwikLok racks to clamp up to 10 x 6mm audio cables per side.
They also work for mains cables, midi cables etc. There's an article and more pics here:
http://www.philizound.co.uk/freebies/audio-wiring/audio-wiring.html
Re-usable tie-wraps are also very useful.
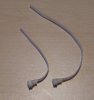
They have a ratchet mechanism so can be released, although this is a bit tricky when you're on the floor reaching round the back of a rack and can only use one hand... but it can be done!
Main cables
4-way sockets tie-wrapped to vertical struts on each rack, leaving the horizontal struts free for audio clamps. One is the 'master' (ideally with individual on/off switches) so only one mains wire enters each rack. Extra 4/6-way sockets fan out from this to power the gear within the rack. The switches allow sections to be isolated for maintenance. More photos in the 'audio wiring' article.
Patch Bays
Labelling was always an issue, especially when things need changing - the layout has gone through several incarnations due to moving house or rooms, and of course buying new gear

Final solution was to use a word processor and print an A4 sheet for several panels, with colour coding as reqd, then laminate the whole sheet and slice it up into strips. Stick the strips on with very small blobs of blue-tack. I tried self-adhesive labels but these make a real mess when things need changing. Small alterations can be marked up with the permanent marker pen, then when too many things have changed, I just edit, reprint & laminate a fresh sheet.
Balanced/Unbalanced
The first layouts used unbalanced cable - managed to acquire lots of RG58 cable from my old place of work as every time they re-wired an office, all the old ethernet cabling was ripped out and scrapped. As long as everything was earthed, I managed to eliminate all hum from almost all the gear even though some of the wires were 10m long. The only issues were certain bits of gear which refused to play ball no matter how short the cables. DI boxes would have solved that, but the other 'niggle' was the mix of signal levels (+4dBu vs -10dBV) and balanced vs unbalanced gear, so eventually I bit the bullet for the next incarnation and changed everything to balanced.
MIDI
Standard balanced patchbays and patch cables are also used for MIDI routing.
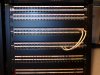
The bottom two patch panels in the photo are an example. There's an article here:
http://www.philizound.co.uk/freebies/midi-wiring/midi-patch-panels.html
Digital routing
I only use a computer for front-end editing and back-end CD burning or MP3 conversions. Everything else is done with a stand-alone hard-disc recorder and analogue mixer and outboard gear, so an old Fostex DP-8 links these digitally with fibre-optic cable and/or coax.
Cable labelling
Some self-adhesive labels can end up being a gooey mess after a few months/years when the glue breaks down (can recommend 'sticky stuff remover' - it does exactly what it says!). Tried an expensive dymo labelling system once - looked really promising with nice neat thermal-printed lettering, but after a couple of years the glue was fine... but all the lettering had faded, doh! Best solution for me was to use light-coloured cables such as white or yellow, and hand-write on the cable using a permanent marker pen. Not as neat as printing, and the ink gradually defuses into the plastic and becomes slightly blurred over time... but they're still perfectly readable after many years - and no glue in sight.
Patch cables
These hangers are really useful - a bit pricey but they'll last forever.
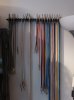
The ones shown here have 10 slots and each slot holds 6 audio cables with 1/4" jacks. The mono patch cables on the right are for the modular synth.